I know some (if not all) of you people really care about what you buy. Although many of us are not engineers, we can tell good designs from bad designs. What we cannot typically tell is what are good materials and bad materials simply by looking at pictures.
Lowering springs can be found by many manufacturers. Many of them claim to use the same materials as “such and such well-known brand”. And they may be correct (since there are several spring manufacturers that let small brands outsource through them). But, some small brands may request a different material to get their price point way way down. These days, a set of good quality springs can average the $275 mark. Anything below that is not necessarily questionable, but I’d be wary of them (unless it is a discounted price from a known brand and reputable retailer, and you can confirm the product is authentic- beware of counterfeits!).
To get right to the point, TEIN uses SAE 9254V, which is a Chrome Silicon Vanadium alloy. This is not an uncommon material. Many well-respected brands state this alloy as their material of choice for their springs.
So, we get this Chrome Silicon Vanadium wire, which is in a “soft” state, and feed it through a machine that first draws out the wire and straightens it, then pulls it through a mandrel that makes the wire diameter consistent. Then we can feed it through our machine to form coil springs.
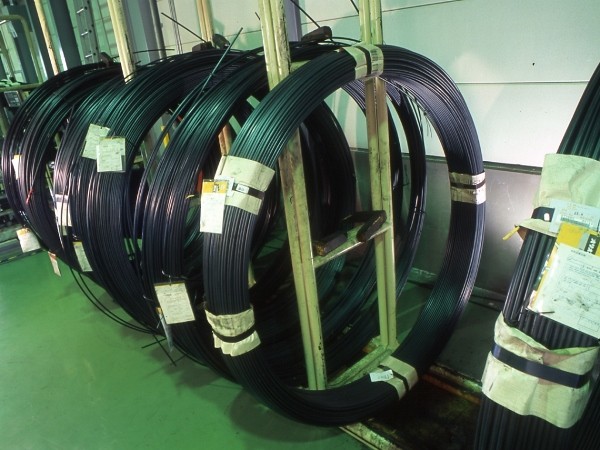
These massive hula hoop looking things are the chrome silicon vanadium steel wire we use for our springs. Still in a relatively soft state, it will be fed through dies to straighten out and ensure consistent diameter before being fed through a computer controlled coiling machine.
Coiling of the wire alloy is done in a cold state (not ice cold, btw). This is done “cold” because most all of our springs are not very large in wire diameter. It’s easy for us to form in such a condition. It’d be a different story if our coil springs were used for trains or huge trucks. This method also eliminates one step- preheating the wire, which can alter the alloys molecular structure and potentially weaken the material.
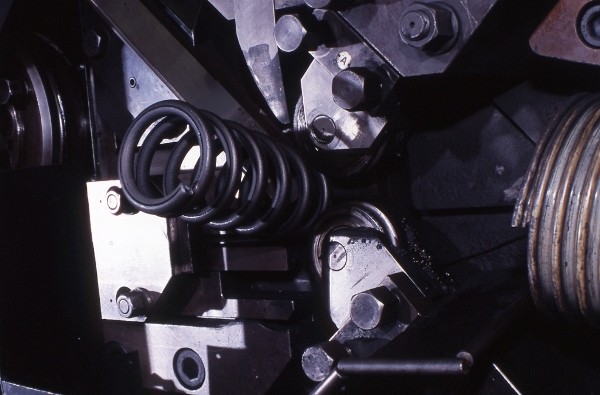
If you’ve read other articles about coil spring manufacturing, you’ll hear it likened to pasta being formed. These computer controlled machines can make adjustments as wire is being fed into the machine, allowing us to make many different shapes of springs, like our taper or barrel springs. This is what sets spring manufacturers apart from one another. Each manufacturer has their own design.
There is still a heat treatment step to follow our process anyway, which is the next step after cold winding. This adds strength to the alloy by realigning the molecular bond of the alloy. Close attention is paid during this step, as it needs to be timed properly and at the correct temperature. Improperly heat treated springs can either sag or break, depending on how long the heat treatment process went.
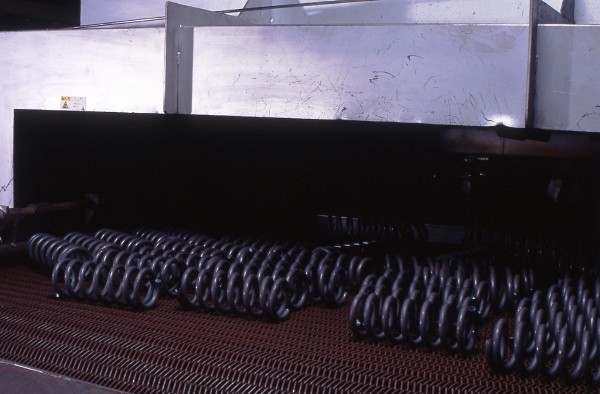
Finished coil springs which have been cut from the coiling machine will next go through heat treatment. Cold forming of the coils can alter the molecular structure of the wire, so heat treating helps to realign this molecular bond prior to the next stages of processing.
Depending on the vehicle application, the next step is flat grinding the spring ends. This is important because this allows the spring load to be evenly distributed across the spring’s surface area. However, this is only an important step if the factory spring design requires flat grinding. In other words, the springs we make must have matching ends to the factory setup in both the spring perch and upper seat assembly.
Our shot peen process is the next step. This takes tiny steel balls (called “shot”) and impacts the spring at high velocity. This is a stress relieving process. Impacting the spring surface is likened to a blacksmith hammering a piece of iron. It shapes and compacts the surface, giving it strength. This, however, leaves the core of the wire spring “soft”. That is what you’d want, because if the inner core of the wire spring is strengthened, it can make it brittle.
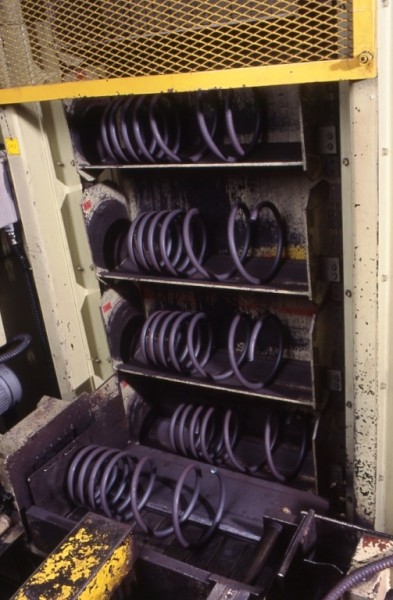
The heat treated coil springs will then be sent to shot peening for stress relieving and surface compaction.
We then go through a Setting process, which puts the spring under load for a specified period of time and at an elevated temperature. This lets the spring settle to the correct length and is also a quality control measure. After setting, we inspect the springs to make sure they fall within specification prior to the final step- powdercoating.
We use a urethane powder paint, but prior to that, we apply a zinc powder base for corrosion resistance. They are baked on at the same time and can last the life of the spring.
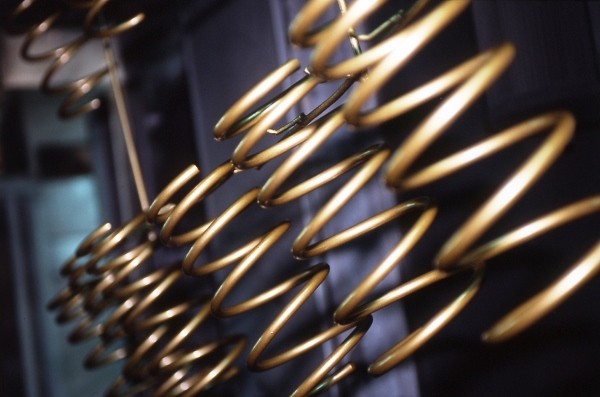
Our 2-stage powder paint process ensures a long lasting spring with excellent surface corrosion protection.
We have a great success rate with our springs. While we do offer a 1 year warranty against spring sag (more than 5mm), it is not to say that a spring will never sag. The repetitive cycling of a spring (compressing and extending) weakens a spring over time. However, the materials and processes we use provide a very long lasting spring. It is not very common for us to see a spring that has sagged, even after years and well over 150,000 miles of use.
Nothing much changes when we manufacture our springs for coilovers. The same processes are used. The only exception is our Racing Spring line.
Racing Springs use a SWOSC-KV material, which offers very similar properties as our SAE 9254V springs, but we can now make a much more lightweight spring. That’s a benefit when trying to keep weight of a race car down. This weight savings is accomplished by winding a spring with less material. The only downside to such lightweight springs is the spring stroke maximum. These have much shorter stroke length for a given spring free length and wire diameter. Exceeding the design’s spring stroke can cause them to sag.
Spring design is critical, for obvious reasons (performance being one of the main ones). But material is just as critical, if not more so. We want to utilize the best material that won’t cost a pretty penny. So, when looking for springs, be picky about the ones you really want. Know that TEIN puts a lot of time to engineer a great performing product at a great value.
As we’ve mentioned, a well engineered spring can make a world of difference, especially in terms of safety.