Enzo Ferrari was once quoted for saying, “Aerodynamics are for people who can’t build engines.” Funny guy, that man. Colin Chapman, however, saw aerodynamics as the future of F1, which reflects heavily on the design direction of the F1 cars you’ve seen for the past four decades. It has been used effectively and with amazing results.
If you follow much on the ever-growing Time Attack racing series, you’ll see or hear about aerodynamics. Other than amazing and tractable power that most engines can be tuned for these days, along with a great suspension and tire package, the only way to tick off several tenths of a second from your lap seems to be crazy aero. Incredibly crazy aero. So much so that the cars on track resemble upside down airplanes. Makes me wonder exactly how much downforce these kitted cars are generating.
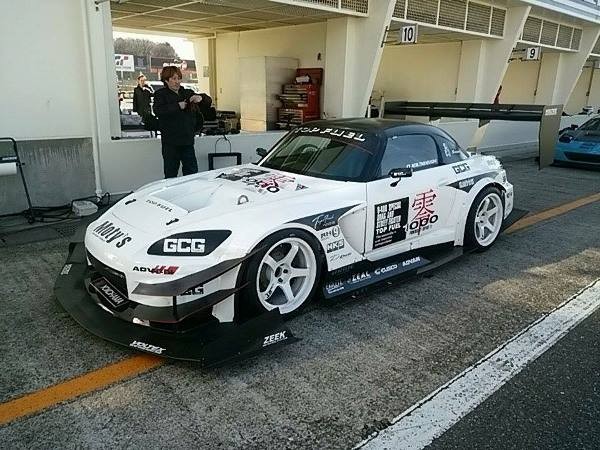
This hammerhead shark looking thing comes from the Top Fuel team in Japan. Currently breaking records at Tsukuba and Fuji Speedway. The front splitter and rear wing are waaaaay too wide for use on the street, which this car will probably never see again anyway. Downforce is what’s keeping these fully prepped unibody cars fast (as well as tons of power).
Aerodynamic tuning seems to be a fairly straightforward approach these days, with many people fabricating their own front splitters, canards, flat bottoms, and rear diffusers. While this post is not necessarily about how aerodynamics work both positively and negatively, it is important to know that it is very effective, and it takes more fine tuning of the rest of your vehicle to make the aero work in harmony with your car.
So how does all this extra downforce from aerodynamic gain affect suspension?
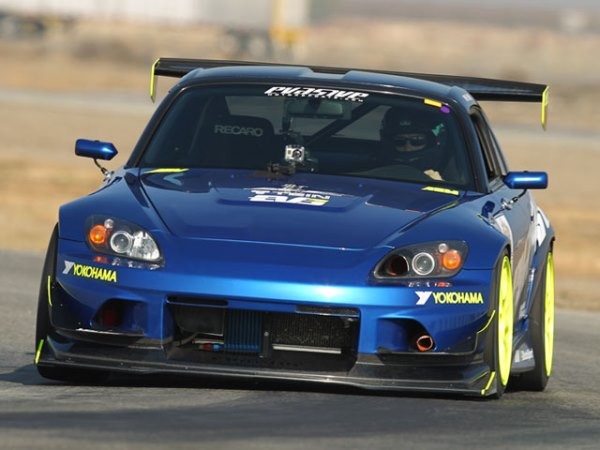
This Evasive S2000 had a full aero package. Front splitter, flat bottom under tray, & rear wing work together to generate sufficient downforce. Using street tires (treadwear 180) and Evasive Motorsports’ own Evasive-Spec TEIN Super Racing dampers, this Street RWD class Time Attack car broke records at Buttonwillow in Street RWD class events.
When we set up a suspension kit for a vehicle, we have to factor several items prior to deciding which spring rates will work best, followed by how we will valve the dampers depending on what the driver experiences. After all, it is the driver’s confidence we’re trying to build up, which in turn translates into a high performing car if they can do their part behind the wheel.
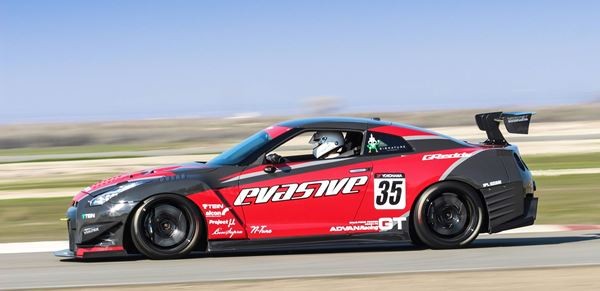
Believe it or not, this GT-R from Evasive Motorsports has relatively mild aero components. Still, it’s a matter of finding the right balance for the vehicle at differing speeds. For us as a suspension manufacturer, we’re always concerned with how the stability of the car is affected through body dynamics, whether under turning, accelerating, or braking (as in this picture).
We also have to take into account what type of ride height the customer wants to achieve, which in turn affects the damper length, including droop/extension and bump stroke. Keep in mind that your steering geometry must be set for that specific ride height, as you want minimal effect in bump steer.
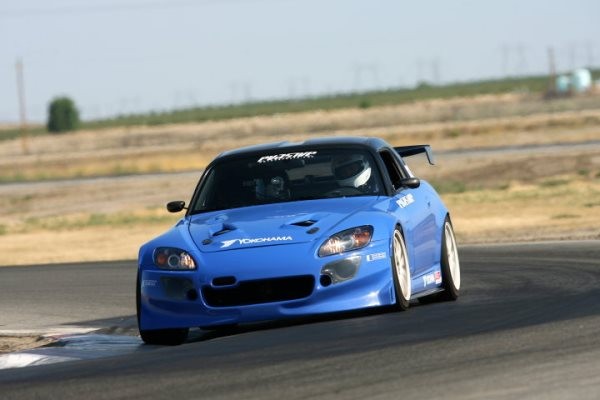
This S2000 going through a turn looks like it is flat relative to the curve. However, you can see that the asphalt is slightly cambered, and the inside wheels/tires need to droop down and maintain contact for greater traction, which it is doing. Otherwise if the wheels were to have lost contact, traction suffers and the balance is thrown off. This car also has relatively mild aero additions.
In its heyday, aero tuning wasn’t understood as it was today. Early reports in F1 stated that the vehicle would oscillate, or “porpoise”, at varying speeds. If the suspension setup was too soft, this problem could be exacerbated by this porpoising phenomenon. This effect disrupts airflow and causes instability as speed increases.
F1 typically has the best examples of the effect of downforce on suspension. For one, F1 cars of today have incredibly stiff suspension. Some control arms actually don’t even have any pivoting point and rely on flexing to provide suspension movement. If you’ve seen an F1 car in action, you’ll know that, for the most part, the circuits they drive on are very smooth. Nevertheless, suspension is still necessary as the car still has to pass through gaps, curbing, etc. However, F1 regulations allow a tire with a really huge sidewall. So this in turn acts as suspension (just without proper damping; also helps create a fairly large contact patch for the tire). If it were tires with a very low aspect ratio (small sidewalls) the car would have to rely on softer suspension, which is what they want to avoid doing.
Still, when you watch an F1 car, you can notice how little body roll there is (it’s noticeable, but not as severe as a street car). The suspension does move, so it is functional. It seems though that the tires, as they deflect and deform through turns, adds to body motion.

Obviously this Sahara Force India car is going past a curb, which makes the car look like there is some body roll. Of course there is some roll, just very minimal.

This older spec Ferrari shows just a bit more body roll at turn-in.
But, on straightaways, it is clear that F1 car suspension is working. Thankfully this has been made clear in the 2015 regulations as all cars must use a titanium skid plate. And when this skid plate makes contact with the ground, it makes an amazing shower of sparks seen coming out the car’s back end. Why is this helpful? because clearly the car is making enough downforce to cause the skid plate to scrape along the ground.
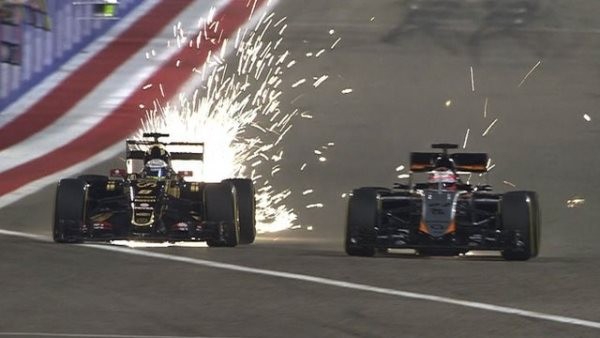
We kinda dig the show current F1 cars put on, especially with their titanium skid plates.
This is a factor that is still important with street cars set up for racing. You may find a need for super stiff suspension, but for the most part we don’t have, or get, to drive on super smooth circuits like F1 cars do. That means we need a suspension that can track the road surface better and help maintain good traction. Super stiff suspension with very little droop travel with literally be skipping off the curbs and bumps. It wouldn’t take a whole lot to make the car feel unsettling. So, therein lies the problem. Then, once you add aero parts like a front splitter, flat bottom, rear diffuser, & rear wing, you’re compounding the problem. It’s a balancing act.
For the most part, our Super Racing dampers are designed and valved with some specific spring rates in mind for each application. In fact, some of our sponsored teams, like SportCar Motion and Evasive Motorsports here in the U.S., have pretty aggressive aero on their Time Attack vehicles, yet they still use our recommended spring rates. Really aggressive aero, and even a change in stickier tires, may require a small change in spring rate, maybe something slightly stiffer (+2kg/mm), and that is more than enough.
Ultimately, it is best to try a suspension kit as-is at our recommendations, do your testing, work on any other additional modifications you make to the vehicle, continue testing, then you can assess what changes you need to make to your suspension. It can be as simple as damping force changes, ride height changes, or spring rate change. Starting with an out-of-the-box setup is at least a good baseline. Just as with any other modification you make to your car, modifications to suspension can also be made. We’ve already spent the time to engineer the the suspension kit for your specific application (albeit a relatively stock vehicle), so that gives you a great baseline to start with.
Since I brought up what Enzo Ferrari said- “Aerodynamics are for people who can’t build engines”, how about this new engine for the 488 GTB:
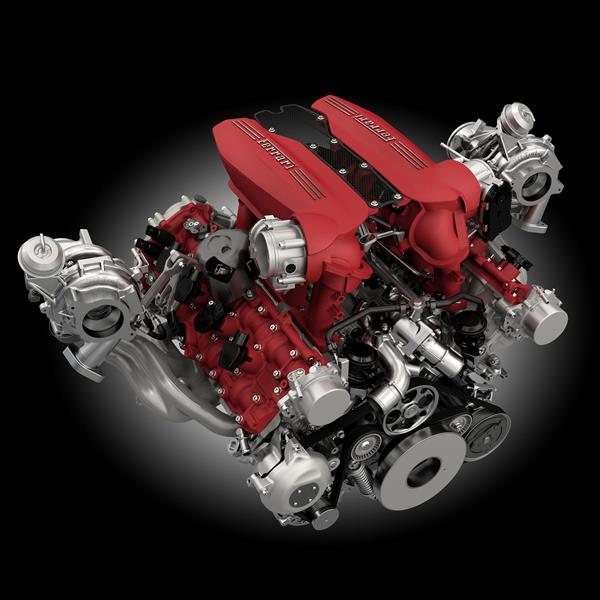
Damn, that looks sexy.
One extra thought- while it’s nice to try and pioneer your own aero setup for your car, sometimes it’s best to go with a tested/developed setup for your car. Piecing together components from different manufacturers, although looking very similar and wanting to create similar effects, may not net the results you are looking for. Aerodynamic tuning can be very tricky to get right, depending on what you want to achieve.
